Nissan Maxima Service and Repair Manual: P0139, P0159 HO2S2
Description
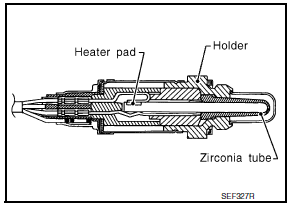
The heated oxygen sensor 2, after three way catalyst (manifold),
monitors the oxygen level in the exhaust gas on each bank.
Even if switching characteristics of the air fuel ratio (A/F) sensor 1
are shifted, the air-fuel ratio is controlled to stoichiometric, by the signal
from the heated oxygen sensor 2.
This sensor is made of ceramic zirconia. The zirconia generates voltage
from approximately 1 V in richer conditions to 0 V in leaner conditions.
Under normal conditions the heated oxygen sensor 2 is not used for
engine control operation.
DTC Logic
DTC DETECTION LOGIC

The heated oxygen sensor 2 has a much longer switching time
between rich and lean than the air fuel ratio (A/F) sensor 1. The oxygen
storage capacity of the three way catalyst (manifold) causes the
longer switching time. To judge the malfunctions of heated oxygen
sensor 2, ECM monitors whether the switching response of the sensor's
voltage is faster than specified during various driving conditions
such as fuel-cut.

DTC CONFIRMATION PROCEDURE
1.INSPECTION START
2.PRECONDITIONING
If DTC Confirmation Procedure has been previously conducted, always perform
the following procedure
before conducting the next test.
- Turn ignition switch OFF and wait at least 10 seconds.
- Turn ignition switch ON.
- Turn ignition switch OFF and wait at least 10 seconds.
TESTING CONDITION:
For better results, perform "DTC WORK SUPPORT" at a temperature of 0 to 30C (32
to 86F).
3.PERFORM DTC CONFIRMATION PROCEDURE
With CONSULT
- Turn ignition switch ON and select "DATA MONITOR" mode with
CONSULT.
- Start engine and warm it up to the normal operating temperature.
- Turn ignition switch OFF and wait at least 10 seconds.
- Turn ignition switch ON.
- Turn ignition switch OFF and wait at least 10 seconds.
- Start engine and keep the engine speed between 3,500 and 4,000 rpm
for at least 1 minute under no load.
- Let engine idle for 1 minute.
- Make sure that "COOLAN TEMP/S" indicates more than 70C (158F).
- Drive the vehicle in a proper gear at 60 km/h (38MPH) and maintain
the speed.
CAUTION:
Always drive vehicle at a safe speed.
- Release the accelerator pedal fully at least 5 seconds.
CAUTION:
- Enable the engine brake.
- Always drive carefully.
- Never apply brake when releasing the accelerator pedal.
- Repeat step 9 and 10 at least 8 times.
- Check the following item of "DATA MONITOR".
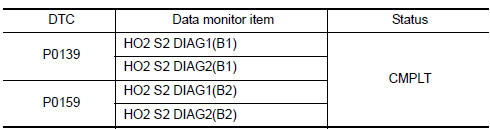
4.PERFORM DTC WORK SUPPORT
- Open engine hood.
- Select "HO2S2 (B1) P0139" or "HO2S2 (B2) P0159" of "HO2S2" in "DTC
WORK SUPPORT" mode with
CONSULT.
- Start engine and follow the instruction of CONSULT display.
NOTE:
It will take at most 10 minutes until "COMPLETED" is displayed.
5.PERFORM DTC CONFIRMATION PROCEDURE AGAIN
- Turn ignition switch OFF and leave the vehicle in a cool place
(soak the vehicle).
- Perform DTC confirmation procedure again.
6.PERFORM SELF-DIAGNOSIS
With CONSULT-III
Perform ECM self-diagnosis.
7.PERFORM COMPONENT FUNCTION CHECK
Perform component function check.\
NOTE:
Use component function check to check the overall function of the heated oxygen
sensor 2 circuit. During this
check, a 1st trip DTC might not be confirmed.
Component Function Check
1.PERFORM COMPONENT FUNCTION CHECK-I
Without CONSULT
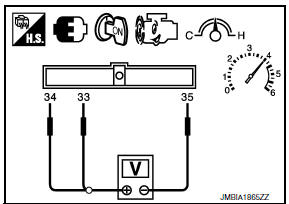
- Start engine and warm it up to the normal operating temperature.
- Turn ignition switch OFF and wait at least 10 seconds.
- Turn ignition switch ON.
- Turn ignition switch OFF and wait at least 10 seconds.
- Start engine and keep the engine speed between 3,500 and 4,000 rpm
for at least 1 minute under no load.
- Let engine idle for 1 minute.
- Check the voltage between ECM harness connector terminals
under the following conditions
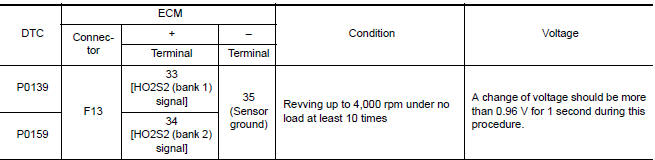
2.PERFORM COMPONENT FUNCTION CHECK-II
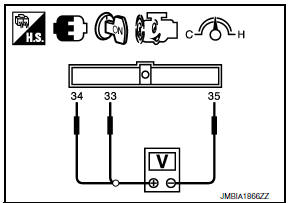
Check the voltage between ECM harness connector terminals under
the following conditions.
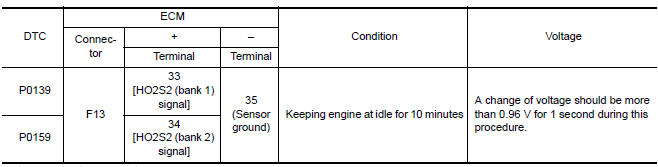
3.PERFORM COMPONENT FUNCTION CHECK-III
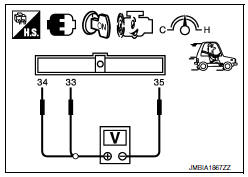
Check the voltage between ECM harness connector terminals under
the following conditions.
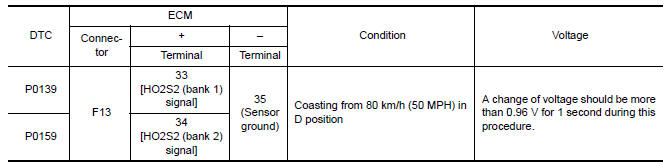
Diagnosis Procedure
1.CHECK GROUND CONNECTION
- Turn ignition switch OFF.
- Check ground connection E9.
2.CLEAR MIXTURE RATIO SELF-LEARNING VALUE
- Clear the mixture ratio self-learning value.
3.CHECK HO2S2 GROUND CIRCUIT FOR OPEN AND SHORT
- Turn ignition switch OFF.
- Disconnect heated oxygen sensor 2 harness connector.
- Disconnect ECM harness connector.
- Check the continuity between heated oxygen sensor 2 (HO2S2)
harness connector and ECM harness
connector.
- Also check harness for short to ground and short to power.

4.CHECK HO2S2 INPUT SIGNAL CIRCUIT FOR OPEN AND SHORT
- Check the continuity between HO2S2 harness connector and ECM
harness connector.
- Check the continuity between HO2S2 harness connector and ground, or ECM
harness connector and
ground.
- Also check harness for short to power.

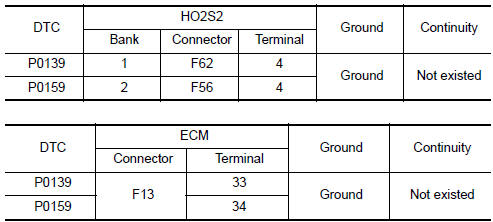
5.CHECK HEATED OXYGEN SENSOR 2
6.REPLACE HEATED OXYGEN SENSOR 2
Replace malfunctioning heated oxygen sensor 2.
CAUTION:
- Discard any heated oxygen sensor which has been dropped from a
height of more than 0.5 m (19.7
in) onto a hard surface such as a concrete floor; use a new one.
- Before installing new oxygen sensor, clean exhaust system
threads using Oxygen Sensor Thread
Cleaner [commercial service tool (J-43897-18 or J-43897-12)] and approved
anti-seize lubricant
(commercial service tool).
7.CHECK INTERMITTENT INCIDENT
Component Inspection
1.INSPECTION START
2.CHECK HEATED OXYGEN SENSOR 2
With CONSULT
- Turn ignition switch ON and select "DATA MONITOR" mode with
CONSULT.
- Start engine and warm it up to the normal operating temperature.
- Turn ignition switch OFF and wait at least 10 seconds.
- Start engine and keep the engine speed between 3,500 and 4,000 rpm
for at least 1 minute under no load.
- Let engine idle for 1 minute.
- Select "FUEL INJECTION" in "ACTIVE TEST" mode, and select "HO2S2
(B1)/(B2)" as the monitor item
with CONSULT.
- Check "HO2S2 (B1)/(B2)" at idle speed when adjusting "FUEL
INJECTION" to +-25%.
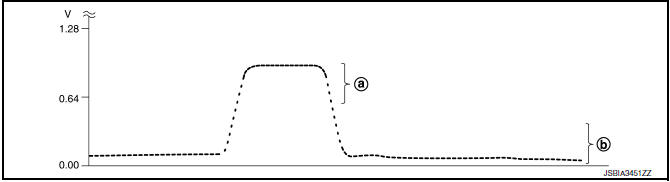
- "HO2S2 (B1)/(B2)" should be above 0.78 V at least once when the "FUEL
INJECTION" is +25%.
- "HO2S2 (B1)/(B2)" should be below 0.18 V at least once when the "FUEL
INJECTION" is −25%.
3.CHECK HEATED OXYGEN SENSOR 2-I
Without CONSULT
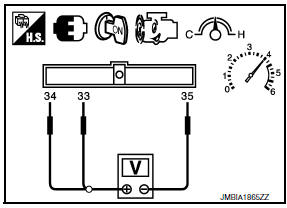
- Start engine and warm it up to the normal operating temperature.
- Turn ignition switch OFF and wait at least 10 seconds.
- Start engine and keep the engine speed between 3,500 and 4,000 rpm
for at least 1 minute under no load.
- Let engine idle for 1 minute.
- Check the voltage between ECM harness connector terminals
under the following conditions.
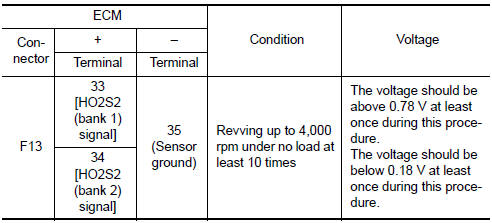
4.CHECK HEATED OXYGEN SENSOR 2-II
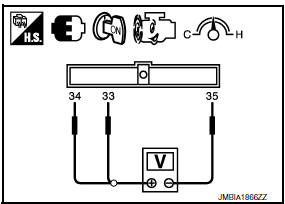
Check the voltage between ECM harness connector terminals under
the following conditions.
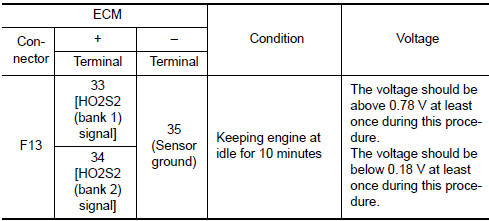
5.CHECK HEATED OXYGEN SENSOR 2-III
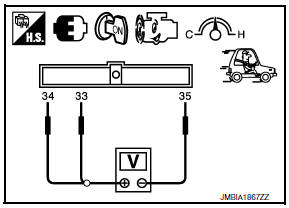
Check the voltage between ECM harness connector terminals under
the following conditions.
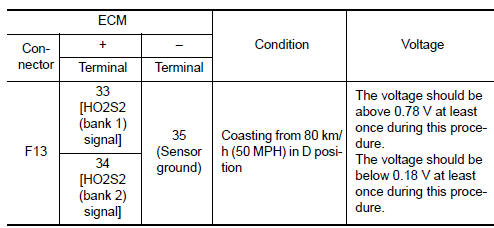
6.REPLACE HEATED OXYGEN SENSOR 2
Replace malfunctioning heated oxygen sensor 2.
CAUTION:
- Discard any heated oxygen sensor which has been dropped from a
height of more than 0.5 m (19.7
in) onto a hard surface such as a concrete floor; use a new one.
- Before installing new oxygen sensor, clean exhaust system
threads using Oxygen Sensor Thread
Cleaner [commercial service tool (J-43897-18 or J-43897-12)] and approved
anti-seize lubricant
(commercial service tool).
Description
The heated oxygen sensor 2, after three way catalyst (manifold),
monitors the oxygen level in the exhaust gas on each bank.
Even if switching characteristics of the air fuel rati ...
Description
The air fuel ratio (A/F) sensor 1 is a planar one-cell limit current sensor.
The sensor element of the A/F sensor 1 is composed an electrode
layer, which transports ions. It has ...
Other materials:
P1615 diffrence of key
Description
Performs ID verification through BCM and Intelligent Key
when push-button ignition switch is pressed.
Prohibits the start of engine when an unregistered ID of Intelligent Key is
used.
DTC Logic
DTC DETECTION LOGIC
DTC CONFIRMATION PROCEDURE
1.PERFORM DTC CONFIRMATION PROCED ...
Precautions on cruise control
1. CANCEL switch
2. RES+ switch
3. SET- switch
4. ON/OFF cruise switch
If the cruise control system malfunctions, it
cancels automatically.
WARNING
Do not use the cruise control when driving
under the following conditions:
When it is not possible to keep the
vehicle at ...
A-bag branch line circuit
Diagnosis Procedure
WARNING:
Always observe the following items for preventing accidental
activation.
Before servicing, turn ignition switch OFF, disconnect battery negative
terminal, and wait 3 minutes or more. (To discharge backup capacitor.)
Never use unspecified tester or other measu ...