Nissan Maxima Service and Repair Manual: Removal and installation
COMPRESSOR
Removal and Installation for Compressor
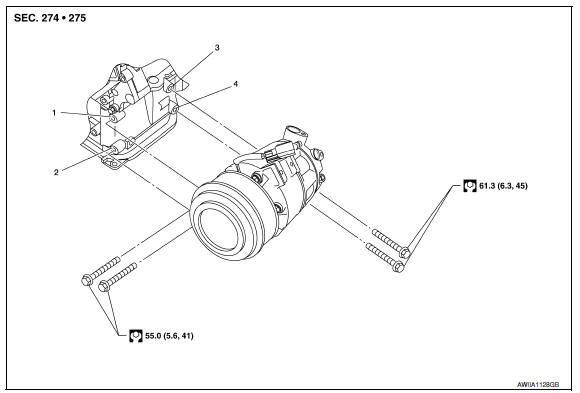
REMOVAL
CAUTION: Before servicing, turn the ignition
switch off, disconnect both battery terminals and wait at least three
minutes.
- Disconnect the battery negative and positive terminals. Refer to
PG-67, "Removal and Installation (Battery)"
- Discharge the refrigerant. Refer to HA-28, "Recycle Refrigerant".
- Partially drain the engine cooling system. Refer to CO-11,
"Changing Engine Coolant".
- Remove the front RH wheel and tire using a power tool. Refer to
WT-60, "Adjustment".
- Remove the engine under cover. Refer to EXT-15, "Exploded View".
- Remove the RH fender protector side cover and the RH fender protector.
Refer to EXT-24, "Removal and Installation".
- Remove the engine room cover.
- Remove the air cleaner assembly. Refer to EM-24, "Removal and
Installation".
- Remove the upper radiator hose.
- Remove the battery and battery tray. Refer to PG-68, "Removal and
Installation (Battery Tray)".
- Remove the engine cooling fan and shroud assembly. Refer to CO-16,
"Removal and Installation".
- Disconnect the high-pressure flexible hose and low-pressure
flexible hose from the compressor. CAUTION:
Cap or wrap the joint of the hose with suitable material such as vinyl tape
to avoid the entry of air.
- Reposition the power steering hose out of the way.
- Disconnect the harness connector from the compressor.
- Release the drive belt tension and reposition the drive belt off
of the compressor clutch pulley. Refer to EM-14, "Removal and
Installation".
- Remove the RH compressor bolts.
- Remove the front compressor bolts using a power tool.
- Disconnect the compressor wire harness clip from the compressor.
- Remove the compressor.
INSTALLATION
Installation is in the reverse order of removal.
CAUTION:
- For installation, tighten the compressor bolts in the order as
shown.
- Do not reuse O-rings.
- Apply A/C oil to the O-rings of the low-pressure flexible hose
and high-pressure flexible hose for installation.
- After charging the A/C refrigerant, check for leaks. Refer to
HA-33, "Inspection".
Removal and Installation for Compressor Clutch
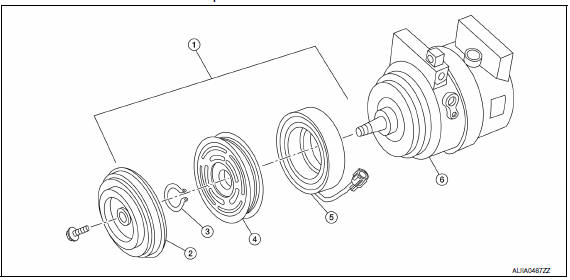
- Magnetic clutch assembly
- Clutch disk
- Snap ring
- Pulley
- Magnet coil
- Compressor
NOTE: Illustrations shown with the
compressor out of the vehicle are for clarity, it is not necessary to remove the
compressor.
REMOVAL
- Remove the front wheel and tire (RH). Refer to WT-60,
"Adjustment".
- Remove the engine under cover. Refer to EXT-15, "Exploded View".
- Release the drive belt from the A/C pulley. Refer to EM-14,
"Removal and Installation".
- Reposition the power steering line aside, do not disconnect the power
steering line.
- Remove the center bolt by holding the clutch disc steady using a
suitable tool.
- Remove the clutch disc and shims.
CAUTION: Retain all the shims for
installation.
- Remove the snap ring using a suitable tool as shown
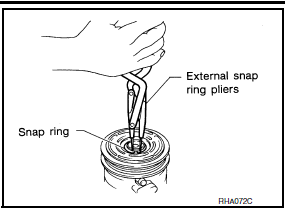
- Remove the pulley assembly using a suitable tool (A) as shown.
CAUTION:
- To prevent deformation of the pulley groove, the puller
claws should be hooked under (not into) the pulley groove.
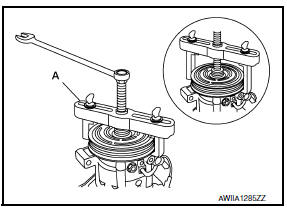
- Disconnect the magnet coil harness.
- Remove the three magnet coil screws using a suitable tool as
shown, then remove the magnet coil.
INSPECTION AFTER REMOVAL
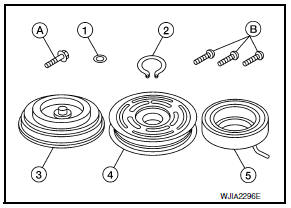
- Shim (1)
- Snap ring (2)
- Clutch disc (3)
- Pulley (4)
- Magnet coil (5)
- Center bolt (A)
- Magnet coil screws (B)
Clutch Disc
If the contact surface shows signs of damage due to excessive heat, replace
the clutch disc and pulley.
Pulley
Check the appearance of the pulley assembly. If the contact surface of the
pulley shows signs of excessive grooving, replace the clutch disc and pulley.
The contact surfaces of the pulley assembly should be cleaned with a suitable
solvent before installation.
Magnet Coil
Check the magnet coil for a loose connection or cracked insulation. Replace
as necessary.
INSTALLATION
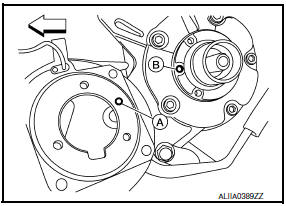
- Install the magnet coil by aligning the magnet coil pin (A) with
the hole (B) in the compressor front head as shown, then install the
magnet coil screws.
: Front
CAUTION:
- Be sure to align the magnet coil pin with the hole in the
compressor front head.
- Connect the magnet coil harness.
- Install the pulley assembly using Tool and a wrench as shown,
then install the snap ring using a suitable tool.
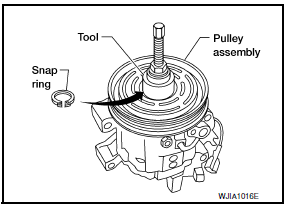
Tool number : - (J-38873-A)
- Install the clutch disc (1) on the drive shaft, together with all of
the original shim(s) (2) using a suitable tool (A).
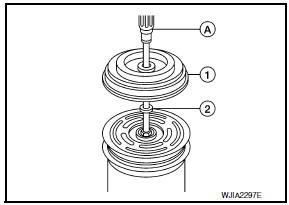
- Install the center bolt using suitable tool.
Center bolt : 12 N*m (1.2 kg-m, 9 ft-lb)
- After tightening the center bolt to specification, check that the pulley
rotates smoothly.
- Reposition the power steering line back into position, do not
disconnect the power steering line.
- Install the drive belt back onto the A/C pulley. Refer to EM-14,
"Removal and Installation".
- Install the engine under cover. Refer to EXT-15, "Exploded View".
- Install the front wheel and tire (RH). Refer to WT-60,
"Adjustment".
INSPECTION AFTER INSTALLATION
Check the clearance (B) all the way around between the clutch disc (1) and
pulley (2) using a suitable tool (A) as shown.
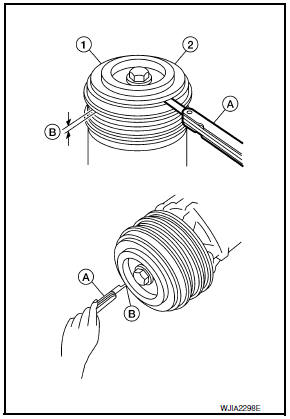
Clutch disc-to-pulley clearance (B) : 0.3 - 0.6 mm (0.012 - 0.024 in)
If the specified clearance (B) is not obtained, replace the adjusting
shim(s) and recheck the clearance (B) as shown.
BREAK-IN OPERATION
When replacing compressor clutch assembly, always conduct the break-in
operation. This is done by engaging and disengaging the clutch about 30
times. Break-in operation raises the level of transmitted torque.
Inspection
INSPECTION PROCEDURE
Connect recovery/recycling/recharging equipment (for HFC-134a) or
manifold gauge.
Start the engine, and set to the following condition.
Maintain tes ...
Exploded View
Heater and cooling unit assembly
High-pressure pipe
High-pressure A/C service valve
High-pressure flexible hose
Air deflector (RH)
Junction pipe
Condenser
Liquid ...
Other materials:
Operating range
The Intelligent Key functions can only be used
when the Intelligent Key is within the specified
operating range from the request switch 1 .
NOTE:
If all doors are already unlocked, opening
the trunk does NOT require an Intelligent
Key to be in range of the trunk request
switch or rear of ...
Front seat
DRIVER SIDE
DRIVER SIDE : Exploded View
Driver Seat - Without Climate Controlled Seats
Headrest
Headrest holder (free)
Headrest holder (locked)
Seatback board
Seatback board clip
Seat cushion inner finisher inside (RH)
Recline mechanism inner cover
Seat cushion outer finis ...
Diagnosis system (audio unit)
Diagnosis Description
Self-diagnosis mode can perform the following items.
Versions display
Channel check diagnosis
Key check diagnosis
AV communication diagnosis
VERSIONS DISPLAY FUNCTION
Turn ignition switch ON.
Turn the audio unit off.
While pressing "1" button, turn vol ...